Custom Applications and Innovations in Wire Wound Resistor
Within the dynamic field of electronic design, wire wound resistors hold indispensable value across a myriad of bespoke applications. While maintaining consistent resistance levels to withstanding thermal variations, these resistors are manufactured to meet contemporary demands of advanced technology landscapes. This narrative explores the adaptation to industry expectations and future exploratory paths within the world of wire wound resistors.
Bespoke Solutions Utilizing Wire Wound Resistors
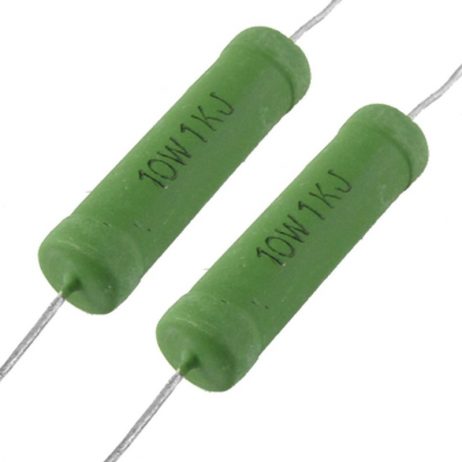
Within unique environments, wire wound resistor s are specifically crafted to meet specific demands. This includes ensuring the correct selection of materials that suit operational desires, whether it's enhanced thermal stability, precise resistive values, or durability.
In contexts requiring swift signal transitions, wire wound resistors are customized to minimize inductance. Achieving minimal inductance involves innovative winding approaches, ensuring coils are evenly spaced and compact. In sound-engineering scenarios, they ensure clarity, fidelity, and noise reduction in audio deliveries, making them ideal for professional sound equipment.
Meeting Regulatory Expectations for Wire Wound Resistors
Meeting standardized requirements is critical in the creation of wire wound resistors. These standards ensure component safety, reliability, and performance in all uses. Standards bodies like IEC and IEEE set forth specifications which must be followed, guaranteeing alignment. For instance, adequate resistive precision is mandated under defined testing conditions, withstand determined power loads, and endure specified environmental conditions.
To ensure compliance, manufacturers employ rigorous testing protocols. Protocols cover resistivity checks, thermal durability trials, and longevity studies. Simulations involving temperature and humidity alterations verify durability and reliability. Adjustments driven by test outcomes provide insight into necessary enhancements, ensuring product evolutionary tracks.
Pioneering Technologies Shaping Wire Wound Resistors
Given the accelerating pace of innovation, these resistors continue to transform, forming the basis for continuous advancement. Developments in materials science lead the charge towards new alloys and core materials, ensuring high resistance, high tolerance capabilities. Advanced algorithms in design software accelerate prototyping and development timelines, opening doors for tailor-made solutions and speedier validations.
Automation plays a crucial role in modern resistor fabrication, wrapping environments, targeting efficiency, stamping uniformity. Mechanized systems align wire securement capabilities, wind shaping, inspection routines. This results in improved throughput, lessens errors. The convergence of tech such as IoT and AI offers futuristic exploration for resistor applications, leading to smart resistors with adaptive functionalities that adjust in real-time scenarios, based on environmental changes, and under operational demands.
Building Sustainable Solutions with Wire Wound Resistors
Building a sustainable future rests heavily on the engineering of resistor component assemblies. Through implementation of earth-centric standards, these resistors are responsible, aligned with audited eco-standards and goals, selective circular structural codes integrated for better service to nature. Whether sourcing sustainable materials or investing in green manufacturing processes, every step counts towards underlining world-friendly educational output in systemic eco-system reflection.
Understanding alliances, between researchers, engineers, and stakeholders, enables both progress and preservation. (to) reaffirm industry and environmental alliances stay firm throughout, solutions are reached that uphold functional excellence while preserving resources. As part of understanding holistic lifecycle connections, (to) couple paths to closing so as to optimize flexibility with achieving long-term equilibrium. Wire wound resistors exemplify in accessing alongside broader eco-conscious desires, undertaking future echoes of wider environmental projects interactions.
The Promising Road to Technological Achievement with Wire Wound Resistor
Resistors form the bedrock as the backbone of modern electronics withstanding expanding testing dimensions and becoming efficient primary companion through the ideas of engineering testing tools.
Any utensil preparing